
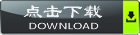
摘要:本研究在以传统生产高炉加入375kg/t的焦炭和160kg/t的煤粉的基础上,采用加入一定量的循环煤气(CO:H2=7:3)来取代煤粉时,分析高炉物料平衡和热平衡变化情况。笔者经过系统的计算公式,编制出物料平衡和热平衡表,得出在富氧率为30%,喷吹循环煤气量为890m3/tFe的条件下即可满足高炉冶炼还原剂和发热剂的需求。该理论为工艺冶炼方案提供理论依据和意见,已达到高炉燃料大幅度降低、降低二氧化碳气体的排放和节约冶炼成本的目的。同时,改善高炉性能、提高碳、氢利用率和提高高炉产量。因此,采用炉顶煤气循环技术对钢铁工业的可持续发展具有十分重要的现实意义和深远影响。
本文通过改变喷吹煤气量、富氧率等条件,分析富氧喷吹循环煤气的物料平衡和热平衡计算结果,绘制相关参数的变化图表,总结出高炉喷吹煤气后热量利用情况和热平衡变化规律:在一定的富氧率下,随着喷吹煤气量的增加,理论燃烧温度降低,其温度变化范围在2060~2100℃之间,变化幅度不大;当喷吹煤气量比较低时,随着喷吹量的增加,直接还原度下降的趋势比较缓慢,当喷吹量较大时,随着喷煤量的增加,直接还原度降低幅度较大。当喷吹煤气量一定的条件下,随着富氧率的提高,冶炼单位生铁需要的风量逐渐减少,但减小的幅度随着富氧率的增加有所减弱。当富氧率低于10%时,风量降低较快;随着富氧率的提高,风量降低趋势有所减缓。
结果表明,采用炉顶煤气循环技术的可行性在理论上得到证实。从新工艺和传统高炉冶炼工艺的工艺参数之间的对比分析结果可以看出:与传统高炉工艺相比,新工艺在许多方面都有着显著的优点:循环煤气不仅降低了焦比,使冶炼生铁所需燃料成本降低53.0元/tFe,其带入的CO和H2使高炉还原性气氛增强、冶炼强度提高、能耗减少、CO2排放量减少,达到了节能减排的目的,具有广阔的应用前景。
关键词:循环煤气 物料平衡 热平衡 冶炼性能
ABSTRACT:The research in the traditional production of blast furnace add 375 kg/t of coke and pulverized coal on the basis of 160 kg/t, by adding a certain amount of circulating gas (CO, H2 = 7:3) to replace the coal dust, the analysis of blast furnace, the change of the material balance and heat balance. Calculation formula of the author through the system, develop the material balance and heat balance, concluded in oxygen-enriched rate was 30%, the injection cycle gas volume of 890 m3/tFe conditions that can meet the needs of blast furnace smelting reductant and compound. The theory provide theoretical basis for smelting process scheme and opinion, has reached to reduce blast furnace fuel, reduce CO2 emissions and save smelting cost. At the same time, improve the performance of blast furnace, improve the utilization rate of carbon, hydrogen, and increase production of blast furnace. As a result, the flue gas recycling technology is adopted to the sustainable development of iron and steel industry has very important realistic meaning and far-reaching influence.
This study by changing the injection amount of gas, oxygen enrichment rate conditions, analysis of rich oxygen blowing cycle gas material balance and heat balance calculations, drawing related parameters change chart, summed up the injection in the blast furnace gas after heat energy utilization and change rule: under the certain oxygen enrichment rate, with the increment of blowing gas, theory burning temperature is reduced, its temperature range between 2060 ~ 2100 ℃, changed slightly; When blowing gas quantity is low, with the increase of injection quantity direct reduction degree of downward trend slowly, and when the larger injection quantity, with the increase of coal injection quantity direct reduction degree is lower too. When blowing gas quantity under certain conditions, with the increase of oxygen enrichment rate, iron smelting unit need air volume gradually decreased, but the extent of decrease with the increase of oxygen enrichment rate reduced. When oxygen enrichment rate lower than 10%, air volume decrease quickly; With the increase of oxygen enrichment rate, air volume decrease trend slowed.
The results show that the flue gas circulation technology feasibility is proved in theory. New technology and the traditional blast furnace smelting process between the process parameters of the comparison and analysis of the results can be seen that: Compared with the traditional blast furnace technology, new technology has obvious advantages in many aspects: circulation gas not only decrease the coke rate, lower the
fuel needed for smelting of pig iron cost 53.0 yuan/tFe, CO and H2 to make it into the blast furnace reducing atmosphere to enhance, improve smelting strength, reduce energy consumption, CO2 emissions, achieved the purpose of energy conservation and emissions reduction, and has broad application prospects.
Key words:Top gas recycling;Material balance;Heat balance;Metallurgical performance