
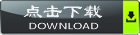
摘要:随着油气管道使用年限的增加,管道腐蚀现象日益严重,造成壁厚减薄,管道承压能力下降,甚至会导致管体局部腐蚀穿孔泄漏或破裂事故的发生。为了预测整个管道的腐蚀情况,确定腐蚀对管道结构完整性的危害程度,确保管道在服役期限内的安全使用。很多国家都已出台相关的评价标准和规范。这些规范形成于不同时期,并且研究的管道强度也不尽相同,为标准使用者带来不便。因此对天然气管线智能检测腐蚀缺陷的比较和评价,可为管道评估人员选取合适评价方法提供参考同时提供决策来确定含缺陷管道是否继续服役维修或更换。本文综述了我国近几年石油、天然气管道防腐技术的应用情况。根据新近的文献报道,从管道腐蚀产生的机理、原因及我国近年油气管道防腐技术应用的现状等方面系统总结论述了管道防腐新技术的应用情况。着重讨论了ASME B31G-2009、RSTRENG、RSTRENG 0.85dl三种智能检测方法的优势和弊端。评价的结果可以计算出了最大安全压力,安全系数以及爆管失效压力,对于排除事故隐患,提升管道管理水平具有重要的意义。
关键词:腐蚀缺陷 智能检测 比较与评价 应用
目录
摘要
ABSTRACT
1 绪 论-1
1.1国内外研究现状分析-1
1.1.1国外研究现状分析-1
1.1.2国内现状分析-2
2 腐蚀缺陷的成因、危害、预防控制措施等现状-3
2.1天然气集输管线腐蚀缺陷形成的原因-3
2.1.1管道所处的地质环境-3
2.1.2管道外腐蚀层影响-3
2.1.3钢管的材质及制造工艺影响-3
2.1.4 输送介质及条件-4
2.2天然气集输管线腐蚀缺陷的危害-4
2.3天然气集输管线腐蚀缺陷的预防控制措施-5
3 腐蚀缺陷常用的评价方法及计算模型-8
3.1 ASME B31G-2009标准-8
3.1.1零级评价-8
3.1.2一级评价-9
3.1.3二级评价-10
3.1.4三级评价-10
3.1.5计算模型-10
3.2 RSTRENG有效面积方法-11
3.2.1计算模型-12
3.3 RSTRENG 0.85dl方法-12
3.4 DNV RP- F101方法-13
3.5 PCORRC方法-15
3.6 APIRP579-2000 标准-15
4 模型实例分析并讨论-17
4.1腐蚀缺陷情况-17
4.1.1确定评价参数-17
4.1.2腐蚀缺陷情况-17
4.2缺陷长度对剩余强度的影响-19
5 结论-22
参考文献-24
致谢-26