
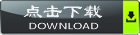
摘要:本文实验研究了锌池中微量合金元素Ni和Ti协同作用对Q235钢热浸镀锌层组织和耐蚀性的影响。将Q235钢分别在Zn-0.03%Ni-0.02%Ti、Zn-0.06%Ni-0.02%Ti、Zn-0.06%Ni-0.03%Ti、Zn-0.06%Ni-0.04%Ti以及Zn-0.05%Ni-0.03%Ti锌池中热浸镀0.5~5分钟,然后用光学显微镜、扫描电子显微镜和能谱分析仪分析了镀层组织结构及厚度的变化,并用电化学方法测试了锌合金在10%NaCl溶液中的耐蚀性。
实验结果表明, 锌池中添加0.03%Ni-0.02%Ti基本能抑制Q235钢合金层的Fe-Zn反应,且随着Ni或Ti含量的增加,抑制效果更加明显。但是当Ti含量大于0.03%时,镀层中会形成溶解有少量Ni的Zn-Fe-Ti三元化合物,且随着Ti含量的增加,三元化合物的量也逐渐增加。本文优化得到最佳的合金元素添加量为0.05%Ni+0.03%Ti。在锌池中添加了合金元素之后,尤其是对硅反应起到抑制作用后,镀层的厚度明显减薄,且合金层的厚度随浸镀时间的增加呈抛物线增加。电化学测试表明,添加0.05%Ni和0.03%Ti后,锌合金的耐蚀性能比纯锌的耐蚀性提高约20%。
关键词:热浸镀锌;硅反应性;镀锌层;合金元素
Abstract: The present work investigated the effect of Ni and Ti on the coating microstructure and corrosion resistance in hot-dip galvanizing Q235 steel. Q235 steel was galvanized in the five kinds of zinc bathes with different Ni and Ti addtion for 0.5 to 5 minutes. The bathes composition are Zn-0.03% Ni-0.02% Ti, Zn-0.06% Ni-0.02% Ti, Zn-0.06% Ni-0.03% Ti, Zn-0.06% Ni-0.04% Ti, and Zn-0.05% Ni-0.03% Ti. The changes of the coating organizational structure and thickness were then analyzed using optical microscopy, scanning electron microscopy and spectroscopy analyzer. And the corrosion resistence of the zinc alloys were investigated by electrochemical corrosion test.
The experimental results show that addition of 0.03% Ni-0.02% Ti into the bath can basicly restrain the Si-reactivity of Q235 steel alloy layer. With increasing Ni or Ti content, the inhibitory ability is more pronounced. However, when the Ti content in bath is more than 0.03%, the coating will form a little of Zn-Fe-Ti ternary compounds dissolving a small amount of Ni. With the increase of Ti content, the amount of ternary of ternary compounds increased. It is believed that addition of 0.05% Ni and 0.03% Ti into the bath is the best one to galvanize Q235 steel. After the alloying elements were added into the bath, especially when the Si reactivity was controlled, the coating thickness was significantly thinned, and the alloy layer thickness increased parabolicaly with the increasing of immerson time. The electrochemical tests showed that after addition of 0.05% Ni and 0.03% Ti, the corrosion resistance of zinc alloy increased by about 20% compared to pure zinc.
Keywords: Hot-dip galvanizing;Si reactivity;galvanized layer;alloy element