
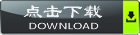
摘要:随着汽车各方面性能的逐渐提高,汽车消费者也在不断要求汽车各个零部件个体 及其匹配性能更加完善。轮胎作为汽车与道路接触的唯一部件,对汽车的动力性、经 济性、操纵稳定性、制动性、舒适性等有重要影响。轮胎刚度作为轮胎最重要的力学 性能,在整车设计分析中不可或缺。目前,考虑轮胎大变形引起的几何非线性,橡胶 材料的物理非线性及接触非线性的三维非线性有限元分析是轮胎性能研究的热点。
本文基于有限元方法研究轮胎的刚度特性。主要仿真轮胎的包覆刚度特性。包覆 刚度能真实的反应出轮胎的包容性。通过对轮胎刚度特性的有限元仿真,有助于设计 出符合最佳刚度特性要求的轮胎。
论文建立在深入研究子午线轮胎结构和材料特性的基础上,针对 175/65R14 型子 午线轮胎,通过 Hypermesh 软件进行网格划分,再使用商业有限元软件 ABAQUS 建 立光面轮胎三维有限元模型。为真实反映轮胎的材料特性,本文采用 Yeoh 模型模拟 超弹性橡胶材料,加强筋模型模拟橡胶-帘线复合材料,进行包覆刚度仿真计算后与 试验值进行了比较,发现仿真结果与试验值较吻合,这就验证了本文采用的包覆刚度 仿真方法是有效性。
关键字:子午线轮胎,包覆刚度,非线性,有限元法,仿真
Abstract:As all aspects of the vehicle's performances enhanced, the consumers also require the performances of individual parts in vehicle and which are matching each other perfectly. Tire as the only part contacted with the road. influenced importantly on vehicle's power, economic, handling, braking comfort performances and so on. Numbers of important performance of vehicle are relative to the mechanical characteristics of tyres, tyre stiffness characteristics also are one of the essential parameters in the whole vehicle design. At present, Considering the nonlinearity of rubber material, geometric nonlinearity and contact nonlinearity using finite element method analysis is the hot study on tire performance.
This article is based on finite element method to simulate the stiffness characteristics of tire, majorly simulating the coating stiffness. Coating stiffness can truly reflect the tire's inclusive. Through the simulations for stiffness characteristics of tire by finite element method, It can help design the tire with best stiffness characteristics.
This paper based on an in-depth study of the radial tire structure and material characteristics for 175/65R14 type radial tire, by Hypermesh software for grid generation, and then use the commercial finite element software ABAQUS establish smooth tires three-dimensional finite element model. As a true reflection of the tire material properties, this article uses the Yeoh model simulating hyper-elastic rubber materials, reinforced model simulating rubber-cord composites, and by comparison with the test results confirm the validity of the simulation method.
Keyword:tire, stiffness analysis, nonlinear, finite element simulation analysis