
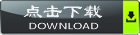
摘要:本设计通过对小型计算器外壳工艺的正确分析,设计了一副一模两腔的塑料模具。在本套模具设计过程中详细地叙述了模具成型零件包括定模板、模仁、动模板、镶块、导杆、斜推杆、滑块等的设计过程,重要零件的工艺参数的选择与计算,及推出机构、浇注系统以及侧向分型、抽芯机构的设计过程,利用当今业界广泛应用的绘图软件pro/E、AutoCAD分析了各方案可行性,并绘出了整套模具,并对成型零件进行了计算。分析并选择了各个成型零件的材料,对其刚度,强度进行了校核,并对试模与产品缺陷作了介绍,最后进行了对模具工艺性与经济性分析。
关键词 计算器外壳;注塑模具;设计
目录
摘要
Abstract
1 绪论-1
1.1 塑料模国内外发展现状-1
2 拟定模具结构形式-3
2.1 确定型腔数量及排列方式-3
2.1.1 塑件成型工艺性分析-3
2.1.2 塑料材料的成型特性-3
2.1.3 脱模斜度-5
2.1.4 型腔数目及排列方式-5
2.2 模具结构形式的确定-6
3 注射机型号的确定-7
3.1 注射量的计算-7
3.2 塑件和流道凝料在分型面上的投影面积及所需锁模力的计算-7
3.3 选择注塑机-7
3.4 注射机有关参数的校核-7
3.4.1 由注塑机料筒塑化速率校核模具的型腔数n-8
3.4.2 注射机的最大注射量校核型腔数量-8
3.4.3 开模行程的校核-8
3.4.4 注射量校核-8
4 分型面位置的确定-10
5 浇注系统形式和浇口的设计-11
5.1 主流道设计-11
5.1.1 主流道尺寸-11
5.1.2 主流道衬套的形式-11
5.1.3 主流道剪切速率校核-11
5.1.4 主流道衬套的固定-12
5.2 分流道设计-12
5.2.1 分流道的布置形式-12
5.2.2 分流道长度-12
5.2.3 分流道的形状、截面尺寸以及凝料体积-13
5.3 浇口的设计-14
5.4 排气槽的设计-15
6 模架的确定-16
7 成型零件的设计与计算-17
7.1 成型零件钢材选用-17
7.2 凹模的结构设计-17
7.3 凸模的结构设计-18
7.4 成型零件工作尺寸的计算-18
7.4.1 平均收缩率计算型腔尺寸-18
7.4.2 按平均收缩率计算型芯尺寸-20
7.5 模具强度的校核-21
7.5.1 整体式矩形型腔侧壁厚度计算-21
7.5.2 整体式型腔底板厚度计算-23
8 导向机构的设计-24
8.1 合模导向零件机构的作用-24
8.2 导柱导向机构-24
8.2.1 导柱-24
8.2.2 导套导-26
9 脱模机构及复位机构的设计-27
9.1 推出机构的组成-27
9.1.1 推出机构的组成-27
9.1.2 推出机构的分类-27
9.1.3 推出机构的设计原则-27
9.2 本模具的推出机构-28
9.2.1 推出机构的选择-28
9.2.2 斜推杆-28
9.3 脱模阻力的计算-29
9.4 复位机构设计-30
10 抽芯机构的设计-31
10.1 机构分类及机构选择-31
10.2 抽拔距与抽拔力及机构组成-31
10.2.1 抽拔距-31
10.2.2 抽拔力-32
10.2.3 滑块-32
10.2.4 导滑槽-33
10.2.5 楔紧块-33
11 冷却系统的设计-34
11.1 冷却系统的计算-34
11.2 冷却系统的结构与布置-35
11.2.1 冷却通道设计的基本原则-35
11.2.2 冷却装置的结构-35
12 塑件质量的分析-37
12.1 合格的塑件应满足的要求-37
12.2 模具性能-37
12.3 次品分析-37
13 注射模具选材-39
13.1 塑料模具成型零件(型腔、型芯)的选材-39
13.2 模板零件的选材-39
13.3 浇注系统零件的选材-39
13.4 导向零件的选材-39
13.5 侧向分型与抽芯机构的选材-39
13.6 推出机构零件的选材-40
13.7 其它零件-40
13.8 该套模具所用材料的性能比较-40
14 模具的试模与修模-41
14.1 试模中遇到的问题-41
14.1.1 粘着模腔-41
14.1.2 粘着模芯-41
14.1.3 粘着主流道-41
14.2 成型缺陷-42
14.2.1 注射填充不足-42
14.2.2 溢边(毛刺、飞边、批锋)-42
14.2.3 制件尺寸不准确-42
15 模具工作过程及工艺性与经济性分析-44
15.1 模具工作过程-44
15.2 工艺性与经济性分析-44
结论-45
致谢-46
参考文献-47